
Empty Corrugate Conveyor (ECC) Systems are conveyors designed to remove corrugate from picking or packing areas to a localized collection point. Trash conveyor is an often used misnomer as ECC conveyor is typical designed for corrugate and not other “trash” items that may be produced in these functional warehouse areas such as plastic wrap. The collection points can often be in a Gaylord for removal or directly into a bailer for compaction and recycling. ECC conveyor systems help eliminate the constant walking to localized trash receptacles and collection of those localized receptacles to a main takeaway center. Cases do not have to be broken down with also helps saves labor. Piece picking and unpacking processes can generate a lot of trash and could result in several Full Time Employees (FTE) only dealing with the trash generated! ECC systems are a fundamental backbone of many operations in a distribution center. It is curious that they are often overlooked during the engineering phase. It is important to make sure your designs are properly engineered so that the trash can be removed at the proper rate without jamming. The last thing your operation needs is to have someone chasing down constant jams on your ECC system!
Need an Expert Opinion?
When should you consider an Empty Corrugate Conveyor System?
Any operation in which empty corrugate is created in any volume can benefit greatly from an ECC system. As labor costs rise the ability to reduce the unproductive time spent dealing with empty corrugate becomes essential. Bailing corrugate for recycling can also help offset the costs of the system itself.
Features
The wide array of ECC conveyor styles and models designed to fit in areas that produce a lot of corrugate such as piece picking, toting, and receiving functions.
- Ceiling hangers with offset connections points
- Angled guard rails make it easy to throw corrugate overhead
- Two pulley hitch design to break a single motor into horizontal and inclined sections
- Varying widths to fit different empty box sizes
- Varying speeds to help feed collection points at the correct volume
Benefits
ECC systems benefit the operations that they interact with by vastly reducing the amount of time and labor it takes to remove high levels of corrugate from a functional area. It also aids in recycling and saves space in congested operations by being overhead.
- Overhead design keeps ECC in functional areas but out of the way of operators
- Eliminates the labor to break down boxes often required for manual operations
- Can be bailed or compacted for easy disposal or recycling
Applications
ECC systems work great in piece picking applications, receiving operations, and toting operations. They can be applied anywhere that corrugate is generated. As operators complete work they simply toss an empty box into the conveyor overhead and continue with their primary function.
- Reduce time spent of trash collection
- Keep operators performing primary function
- Reduce waste by making recycling easy and more economical
ECC Specifications
- Nominal Widths between Frames (BF): 16”, 22”, 28”, 34”, 40” & 46”
- Maximum Product Loading: 50 lbs./ft or 75 lbs. per product
- Operating Temperature: 35° to 120°F
Mechanical Characteristic
- Horizontal Slider: A formed slider pan between channel frames with welded bed connectors and painted crossmembers make up the frame. Return rollers are 1.9“ diameter, with precision bearings and 7/16“ hex axles.
- Frame: 7–1/2“ channel (belt low) has 12 gauge. formed steel side channels 7–1/2“ deep x 1–5/8“ flanges bolted-in crossmembers and welded bed connectors. Frames are painted job color.
- End Pulleys: 2.5” diameter DOM tubing, 11/16” axle, 6205 sealed bearing.
- Drive Bed: 3-phase 60hz In-line high efficiently helical gearmotor with self-aligning rolling cam take-up, brake motor provided as an option.
- Maximum OAL: 150’ with standard drive and take-up, 200’ with an auxiliary belt take-up Belt Types: Belt: Longitudinal rub top monofilament full width belting used for ECC.
- Double Snubber: The double snubber bed will transition the ECC from horizontal conveying to a pitched angle of up to 13 degrees without adding a second belt.
- Guardrail: ECC comes with flared or straight guard rail for capturing product.
- Supports: The ECC can be floor mounted or ceiling supported using a low profile anger that eliminates the extended support pipe into operator areas.
Why Work With Conveyco
Conveyco has been applying conveyor to order fulfillment systems for over 40 years. Our engineering department can apply ECC conveyor correctly to minimize capital expense while keeping the system functioning as needed. There is a fine line between minimizing costs without giving away functionality. Each situation is different, and Conveyco knows where conveyor capital is best spent, and where the opportunities for value engineering exist. ECC systems are often an afterthought, but our engineering team understand the importance of doing things correctly, and the pain that is caused by improper design. Conveyco has spent decades building relationships with the best in breed conveyor lines to allow a wide array of tools curated to pick the manufacturers that best fit each application.
Conveyor System Resources

Accuglide Conveyor: Common Repairs, Upgrades & Spare Parts

TGW Conveyors: Common Repairs, Upgrades & Spare Parts
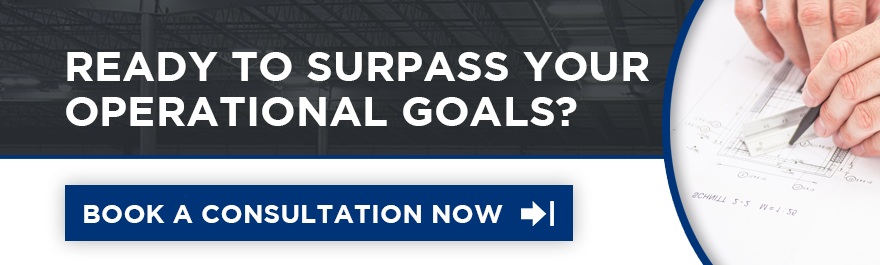